We’ve mentioned the three Ds of medical device manufacturing previously on this blog; they play a significant role in bringing any device to the market and they each need to be carefully managed throughout all of the design and manufacturing processes. In simple terms, a DHF (Design History File) marks the start of a particular device and documents how an OEM arrived at the final design. A DMR (Device Master Record) details the specific material, equipment, and environment requirements for production. The manufacturer maintains a DHR (Device History Record) which has all the documentation of the production process such as date produced, quantity, and labels of the final products.
Let us take a closer look at what each of them entail:
Medical Device Companies (OEMs) will design and develop their product either internally or with the aid of an outside engineering firm. The process will be recorded in a DHF maintained by the OEM.
DHF (Design History File): the collection of documentations created as you go through the design and development processes that documents the evolution of the design including user needs, design inputs, reviews, risk assessment, a plan for making the device which could include manufacturing processes, verification, validation protocols and reports etc. It should contain or reference the records needed to demonstrate that the design developed is in accordance with the approved design plan and the requirements of 21 CFR Part 820.30. Any future changes to the original design will also need to be reflected by updating relevant files.
The DHF will need to be submitted to the FDA at this point, along with its documents, for either a 510k (Some Class I devices and most Class II devices) or Pre-Market Approval or PMA (Class III devices). The FDA reviews the design and product for safety and efficacy, and has the final say on whether or not the product is approved for market.
After obtaining FDA approval, the OEM can move forward and start manufacturing the product in-house or entrust an experienced contract manufacturer like Sanbor Medical. We will work with the OEM during the process to ensure the next set of records are managed in accordance with FDA requirements.
DMR (Device Master Record): a compilation of the procedures and specifications for making the finished device and testing it, including design specifications (drawings, composition, formulation, component and software specifications), process documents, tools and tooling specifications, production methods, environment specifications, inspection procedures, quality assurance (acceptance criteria, QA equipment), labeling and packaging, and service details. Many of these files should be already available if a proper DHF was created, and they can be simply referenced here. The focus is to ensure that the manufacturer has all of the necessary items to build, test, package, and maintain the device.
DHR (Device History Record): the production history of a finished device. Includes: lot #s or UPCs (important for complaint investigations), manufacturing dates, quantity manufactured and distributed, acceptance records that show the design followed the DMR, and labeling for each unit. If the OEM gets audited, the investigator may wish to see a DHR and compare it to the corresponding DMR to check for compliance. If a contract manufacturer is used during this process, the DHR has to specify who reviews and releases the product.
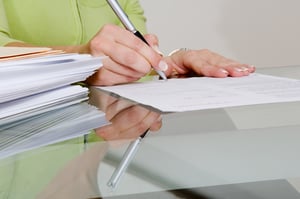
Efficiently managing the three Ds is crucial for regulatory compliance. An OEM will start with a DHF for each type of their devices, collecting documents as the design process moves along. Then for the manufacturer comes the DMR which is essentially all the procedures and specifications on how to actually build the device, according to all the design inputs in the DHF. When the device is actually put into production, the DHR is maintained to show that everything follows the DMR. Since each of these collections of files and records relies on the completeness of the previous files, if any necessary documents were missing, it would greatly affect later documentations and references. If the OEM provides all the necessary documents, Sanbor Medical can deliver the exact same product as the OEM would if they were building it in their in-house facility.
